Anodic Oxidation
Anodizing, also known as anodic oxidation, is a process of surface treatment for metals, especially aluminum, that enhances their resistance to corrosion, creates an aesthetic appearance, and increases their wear resistance. This process involves the artificial creation of an oxide layer on the surface of an aluminum alloy, and this layer has several advantages:
- Corrosion Resistance: The oxide layer protects the metal from exposure to the external environment, such as moisture, chemicals, and corrosive substances.
- Wear Resistance: Anodized surfaces are harder and more resistant to damage compared to untreated metal.
- Aesthetic Appearance: The anodizing process allows for the application of various colors and surface finishes to the aluminum surface, enabling the creation of attractive and decorative appearances.
The anodizing process typically includes the following steps:
- Surface Preparation: The aluminum surface is usually immersed in a series of baths to thoroughly remove natural corrosion, impurities, and grease.
- Anodic Oxidation: A thin and porous oxide layer is formed on the surface of the aluminum material by applying an electric current in an electrolyte.
- Dyeing: The pores of the oxide layer can be used to color the material, achieving a decorative appearance. Various substances and processes are used for dyeing.
- Sealing: As a final step in anodizing, the porous surface can be sealed, closing the pores of the oxide layer, which prevents subsequent contamination of the anodized surface and fading of the color.
Anodizing is frequently used in industry, especially in the production of automobiles, aircraft, electrical equipment, construction materials, and many other applications where increased surface durability, resistance to corrosion, and aesthetic appearance are required.
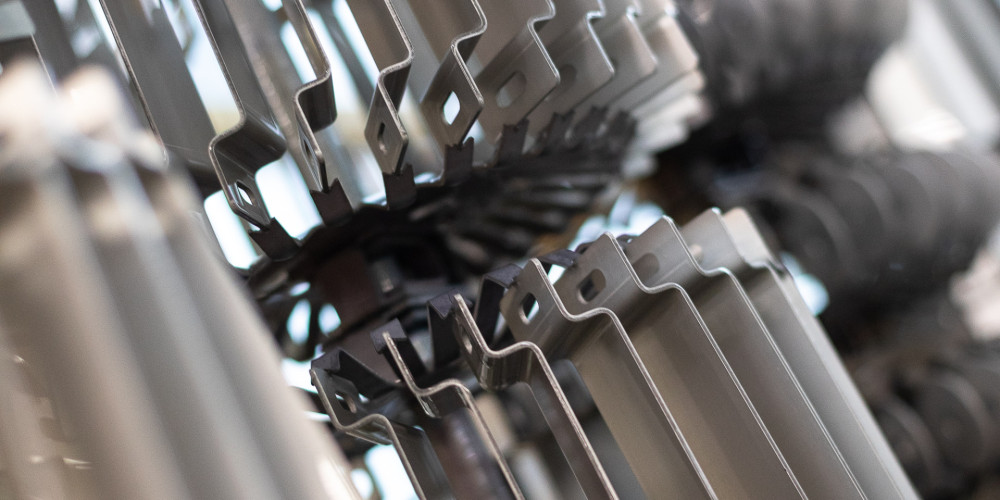